lg220 Melamine Glazing Powder on Decal Paper
Melamine Glazing Powder is also a kind of melamine resin powder. During the production process of glaze powder, it also needs to be dried and ground. The biggest difference from melamine powder is that it does not need to add pulp in kneading and coloring. It is a kind of pure resin powder. Melamine glazing powder is used to put on the tableware or on the decal paper to make tableware shining.
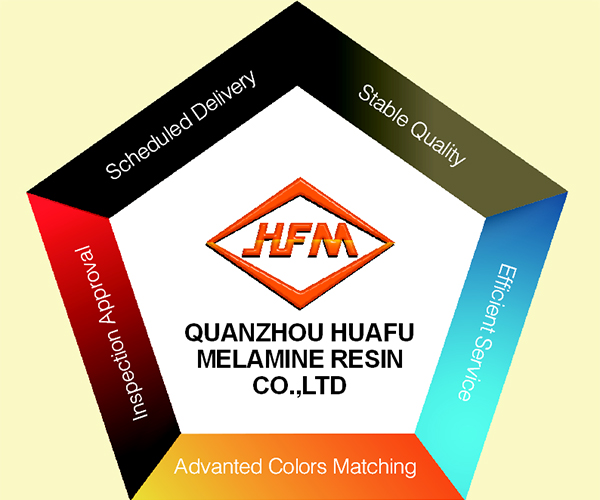
Glazing Powders have:
1. LG220: shinning powder for the melamine tableware products
2. LG240: shinning powder for the melamine tableware products
3. LG110: shinning powder for the urea tableware products
4. LG2501: glossy powder for foil papers
HuaFu has the best products of the Crown of Quality in the local industry.
Physical Property:
Glazing Powder: non-toxic, tasteless, odorless, is ideal amino molding plastic material after-Clear, with light to make the product wear, etc. The article coated with melamine glazing powder has shinny and harder surface and resists better to cigarette burns, foodstuffs, abrasion and detergents.
Advantages:
Good surface hardness, gloss, insulation, heat resistance, and water resistance
Bright color, odorless, tasteless, self-extinguishing, anti-mold, anti-arc track
Qualitative light, not easily broken, easy decontamination, food contact
Applications:
It scatters on the surfaces of urea or melamine tableware or decal paper after moulding step to make tableware shinning and beautiful. When used on tableware surface and decal paper surface, it can increase the degree of surface brightening, makes the dishes more beautiful and generous.
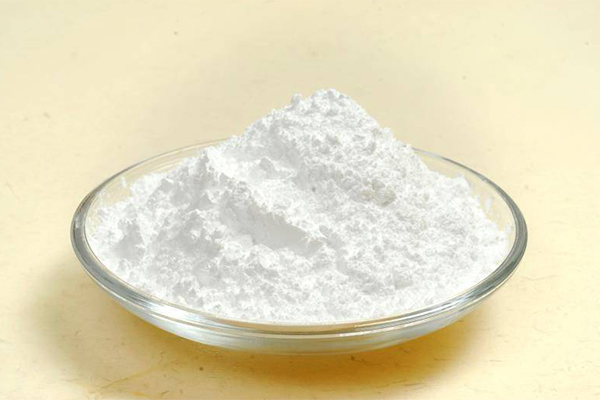
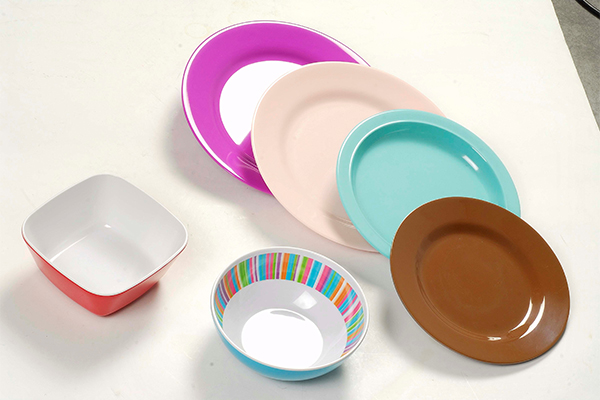
Storage:
Keep containers airtight and in a dry and well-ventilated place
Stay away from heat, sparks, flames and other sources of fire
Keep it locked and stored out of reach of children
Stay away from food, drinks and animal feed
Store according to local regulations
Certificates:
The testing result of submitted sample (White Melamine Plate)
Test Method: With reference to Commission Regulation (EU) No 10/2011 of 14 January 2011 Annex III and
Annex V for selection of condition and EN 1186-1:2002 for selection of test methods;
EN 1186-9: 2002 aqueous food simulants by article filling method;
EN 1186-14: 2002 substitute test;
Simulant used | Time | Temperature | Max. Permissible Limit | Result of 001 Overall migration | Conclusion |
10% Ethanol (V/V) aqueous solution | 2.0hr(s) | 70℃ | 10mg/dm² | <3.0mg/dm² | PASS |
3% Acetic acid (W/V)aqueous solution | 2.0hr(s) | 70℃ | 10mg/dm² | <3.0mg/dm² | PASS |
95% Ethanol | 2.0hr(s) | 60℃ | 10mg/dm² | <3.0mg/dm² | PASS |
Isooctane | 0.5hr(s) | 40℃ | 10mg/dm² | <3.0mg/dm² | PASS |
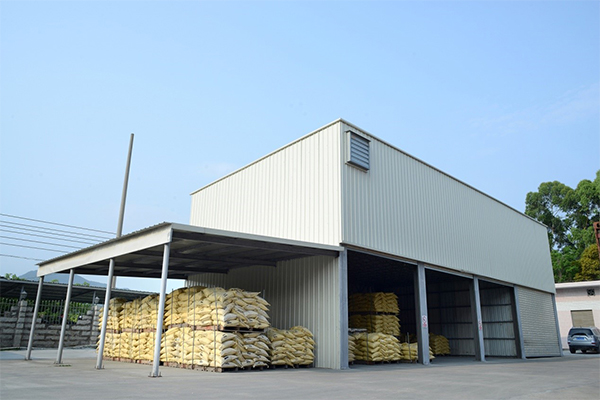
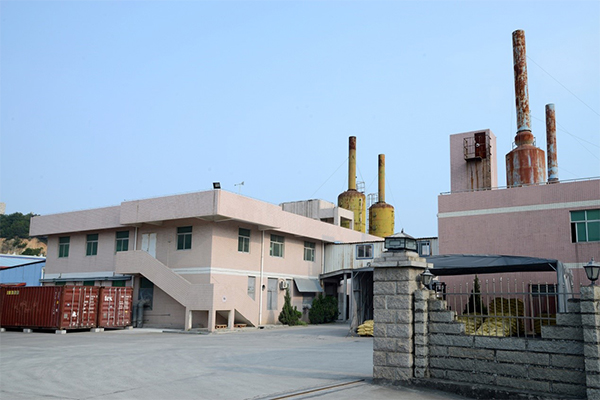
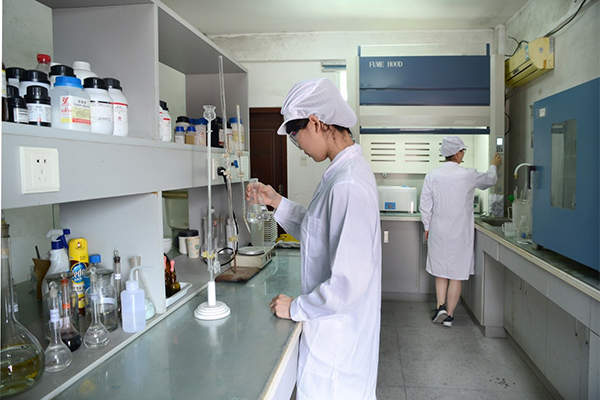
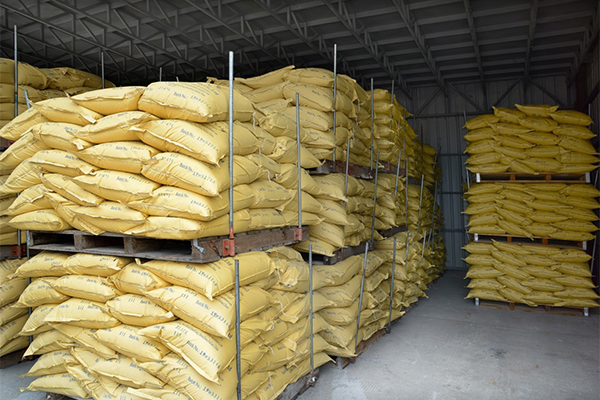